MEET OUR RESTORATION EXPERT SPEAKER
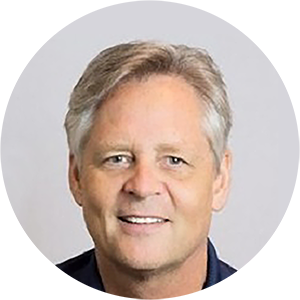
KEN LARSEN
CR, WLS, FLS, CLS, CMP, CSDS, Senior Consultant to the IDSO family of companies:
DryStandard Software, REP, DSi, RTPE and RLI
Ken Larsen has been in the restoration industry since 1978, distinguishing himself as a thought leader and top trainer in restorative drying sciences.
He aims to improve the credibility of the restoration industry with trustworthy technical information and encourage others to embrace it. His specialties? Restorative drying sciences. Technical consulting in structural restoration. Expert witness services.
So we asked him, what are 10 things—in no particular order— that you wish every restorer knew, or did, when tackling tough jobs.
Preparing for peer reviews: What you need to know
When the insurer tells your customer, the policy holder, that they are sending a “peer reviewer” to the property and to review the file, the contractor should prepare the policy holder with some requirements before allowing this peer reviewer access to the property. They aren’t always qualified to be called your “peer.”
The truth about Category 1 losses
Category 1 losses are exceedingly RARE in our industry. Yet, most jobs are being addressed as if they are Category 1. What are the implications for all involved when the job is incorrectly categorized? Why aren’t restorers using their indoor environmental professional (IEP) like a standard job should? Note, your mold consultant may not know how to conduct a category test.
Stabilization vs. drying strategy: Understanding the difference
Study and understand the difference in objectives between a stabilization strategy and a drying strategy. Related point: the initial dehumidification formula has absolutely NO RELEVANCE in a stabilization strategy. Those who use the formula in stabilization are likely to lose their defense of their process.
The misconception of equipment decontamination charges
Why do people charge for “equipment decontamination” of their air movers when they address a Category 2 or Category 3 water loss? Surely, they would NEVER install air movers on the property when it was still contaminated – right? So, what contaminated the air movers?
Why testing dehumidifier and air filtration device performance is crucial
We have finally learned the importance of testing the dehumidifier outputs to establish the machine’s correct operation and performance. Yet, we install Air Filtration Devices on our projects and nobody ever checks them for performance or correct running operation. Why do we fail to document their performance? I check them regularly… and you would be astonished how few of them are actually working as they should. That’s a disservice to all involved.
Machines don't dry buildings: The value of skilled labor
Machines do NOT dry buildings — just as surely as the wrench and ratchets found in a toolbox do not “fix cars.” The mechanic’s skilled use of the ratchet and wrenches produce the desired results. Restorers must be more than merely an equipment delivery service. That’s unskilled labor… and true restoration professionals distinguish themselves from equipment delivery services.
Navigating contentious claim settlements with expert support
While it is important for restorers to have solid education in their trade – like IICRC, RIA and ACAC – the state of the industry has made claim settlement practices so contentious and quarrelsome, that the best way to manage the anticipated dispute is to surround your client, the policy holder, with the industry’s finest experts to defend your processes.
Building indisputable evidence for insurance claims
Insurance claims that are simply paid without dispute are now an anomaly. Therefore, the claims that survive attack are the ones that have the most robust, indisputable evidence from cradle to grave.
The importance of comprehensive documentation in restoration
I’m not just talking about drying records. I’m saying:
- Files with daily emails with read / forward / delete receipts outlining a running total and a request for a claim representative response
- Hundreds, even thousands of photos of the project underway
- A host of other documents that even exceed the S500 2021’s list mentioned in Section 9.
Crafting the narrative: Proving your role in claim resolution
Our industry is less about the end product and much more about the narrative, establishing who dropped the ball on the claim. And be sure someone is going to allege the ball was dropped — so you must be able to prove it wasn’t you.
Water Damage Restoration Bootcamp
4 IICRC CE CREDITS
Break down the complexities of restorative
drying with practical knowledge from experts.
Gain confidence, dry buildings, document
your work and get paid.